To ensure the safe operation of cranes, various safety protection devices are installed. These devices are crucial for preventing accidents and maintaining stability during lifting operations. Below, we discuss seven essential safety devices that enhance crane operation security:
1. Load Indicator
The load indicator is installed on the side of the main boom (typically on the right side of the operator’s cabin). This positioning allows the operator to clearly observe and accurately determine the crane’s working conditions. The indicator provides real-time information about the boom’s inclination angle and the corresponding rated load capacity under specific working conditions. By monitoring this device, the operator can ensure that lifting operations remain within safe load limits, preventing overloading and potential structural failures.
2. Hook Overwind Protection Device
When the hook reaches its designated maximum lifting height, it makes contact with a limit-weight hammer. This contact activates a travel switch, triggering the “overwind” indicator light. Simultaneously, the device automatically disconnects the lifting, boom extension, and boom lowering functions to prevent unsafe movements. To resume normal operations, the operator must lower the hook, retract the boom, or raise the boom, releasing the limit-weight hammer from its engaged position. In special circumstances requiring minor overwind operations, the operator can press the release button on the control panel. Sin embargo, such operations must be performed with extreme caution to avoid accidents.
3. Boom Extension and Retraction Safety Device
If an accident occurs in which the high-pressure hose or hydraulic pipeline in the boom extension and retraction system bursts or is severed, the balance valve within the hydraulic circuit of the boom safety device is activated. This valve locks the hydraulic oil in place, preventing uncontrolled boom retraction and ensuring operational safety. This feature is critical in preventing sudden, unintentional boom movements that could cause instability or structural damage.
4. Load Capacity Chart and Safety Monitoring System
Located on the front lower wall of the operator’s cabin, this chart provides detailed information about rated load capacities, boom lengths, and working radii. Operators must reference this chart during lifting operations to ensure compliance with load limits. Under no circumstances should the operator exceed the specified values, as this could lead to equipment failure or tipping hazards. To further enhance safety, cranes are equipped with advanced monitoring systems that alert the operator to potential risks. These systems either restrict unsafe operations or provide warnings when operating conditions approach critical limits.
5. Outrigger Safety Locking System
During an accident involving a rupture or severance of high-pressure hoses or hydraulic pipelines leading to the vertical outrigger cylinders, the hydraulic system’s bidirectional hydraulic lock engages. This lock seals the pressure oil in both chambers of the outrigger cylinder, preventing unintended retraction or extension of the outriggers. This mechanism is crucial in maintaining crane stability, especially when operating on uneven or unstable ground. It ensures that the crane remains securely positioned, reducing the risk of tipping or loss of control.
6. Hydraulic System Overload Protection
The crane’s hydraulic system is equipped with various relief valves that regulate and suppress abnormal high pressure within the hydraulic circuit. These valves protect the hydraulic pump, motor, and associated components from excessive stress, preventing overloading and ensuring long-term equipment reliability. By maintaining controlled hydraulic pressure, these devices prevent sudden failures that could lead to hazardous operational conditions.
7. Boom Angle Safety Locking System
In the event of a rupture or disconnection of high-pressure hoses or hydraulic lines within the boom angle adjustment system, the balance valve in the hydraulic circuit is activated. This valve locks the hydraulic oil, ensuring that the boom does not unintentionally lower. This feature is critical in preventing the boom from collapsing unexpectedly, which could endanger personnel and equipment. By maintaining the boom in a fixed position until proper repairs can be conducted, this system ensures continued safety during crane operations.
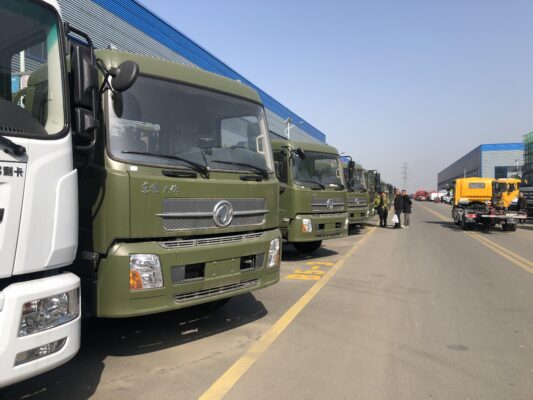
Extended Discussion on Safety and Operational Precautions
Cranes are complex machines that require rigorous safety measures to function effectively. The seven safety devices mentioned above play a crucial role in maintaining operational security. Sin embargo, safe crane operation also depends on proper maintenance, adherence to load limits, and operator training. Below are additional considerations for safe lifting operations:
1. Regular Inspection and Maintenance
Cranes should undergo regular maintenance and inspection to ensure all safety devices function correctly. This includes checking the hydraulic system, inspecting the condition of hoses and pipelines, and ensuring all mechanical components are in optimal working condition. Any signs of wear or damage should be addressed immediately to prevent accidents.
2. Operator Training and Certification
Only trained and certified personnel should operate cranes. Proper training includes understanding load charts, recognizing the limitations of the equipment, and knowing how to respond to emergency situations. Operators must also be familiar with the specific safety devices installed on their crane model.
3. Load Stability and Weight Distribution
Before lifting, the operator must ensure that the load is properly secured and balanced. Uneven or improperly secured loads can cause instability, leading to tipping hazards or mechanical failures. The load must be within the crane’s rated capacity, and external factors such as wind conditions should be considered.
4. Environmental and Site Considerations
Operating a crane in adverse weather conditions, such as high winds or heavy rain, can significantly impact stability and safety. Además, the ground conditions must be stable and capable of supporting the crane’s weight. Outriggers should always be fully extended and secured to provide maximum stability.
5. Emergency Response Preparedness
Operators should be trained to handle emergency situations, such as hydraulic failures, load shifts, or sudden equipment malfunctions. A well-prepared response can prevent minor issues from escalating into major accidents. Cranes should also be equipped with emergency stop mechanisms that allow operators to quickly shut down operations in case of imminent danger.
6. Use of Additional Safety Accessories
Apart from built-in safety devices, additional accessories such as warning lights, sirens, and safety barriers should be used to alert workers in the vicinity of crane operations. Personal protective equipment (PPE), including helmets, gloves, and high-visibility vests, should be worn at all times when working around cranes.
7. Compliance with Safety Regulations
Cranes must comply with local and international safety standards, such as those established by the Occupational Safety and Health Administration (OSHA) and other regulatory bodies. Regular inspections by authorized personnel ensure compliance with safety protocols and help prevent accidents.
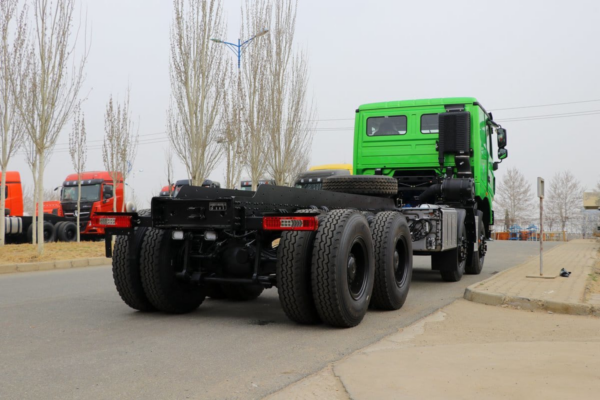
Conclusión
Ensuring crane safety requires a combination of well-designed safety devices, operator awareness, and strict adherence to maintenance and operational protocols. The seven safety devices discussed provide essential protection against common hazards, but their effectiveness depends on proper usage and regular inspection. By implementing comprehensive safety measures, crane operators and site managers can create a secure working environment, reducing the risk of accidents and enhancing overall operational efficiency.